3D Printed Hydrogel Sensors on Deformable surfaces

-
We modeled the deformation of the target surface using a shape basis model that can be learned from a dataset of 3D scans. With the learned shape model, accurate surface geometry can be recovered in 3D via a set of markers tracked by a stereo-vision system. The recovered geometry is used to dynamically adapt the 3D printing toolpath in real time.

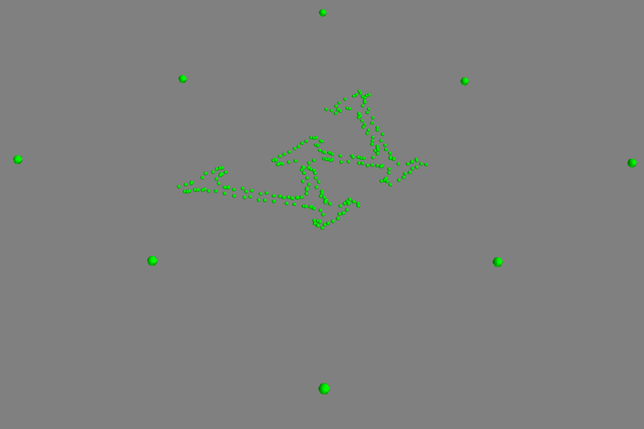
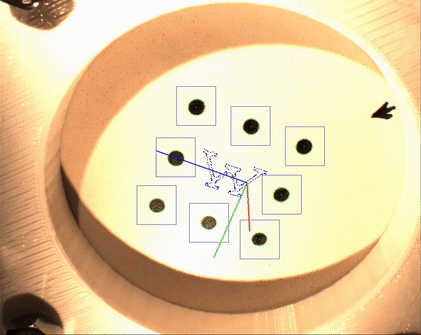
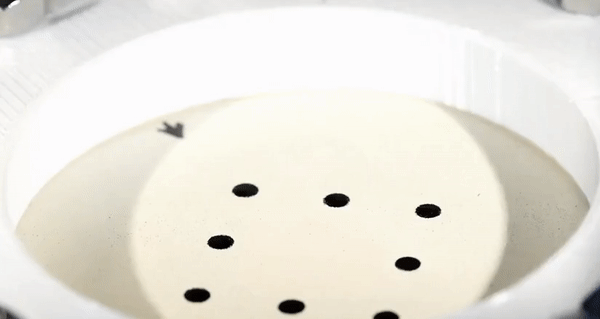
Deformation model
learned via PCA
Camera view with
re-projected toolpath
Printing U of M logo
on a deformable surface
-
We incorporated an ionic hydrogel with electrical impedance tomography (EIT) technology to enable 3D-printed wearable sensors for in situ spatiotemporal mapping of 2D volumetric strain

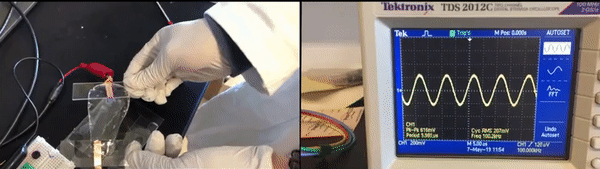
Transparent, strain-responsive hydrogel with tissue-like stretchability

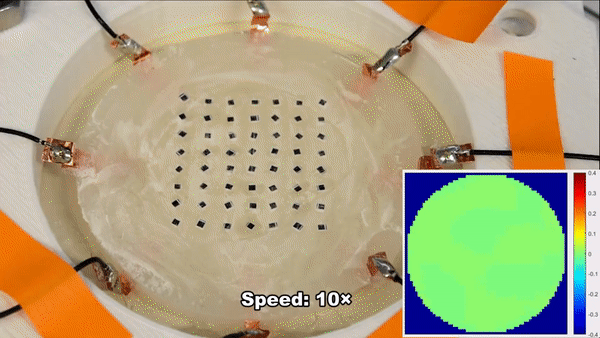
Hydrogel-based EIT sensor for real-time strain mapping
-
To demonstrate the closed-loop 3D printing system for real-time tracking of target deformation, a hydrogel-based EIT strain sensor was directly 3D printed on a breathing lung for in situ monitoring of deformations.
_JPG.jpg)

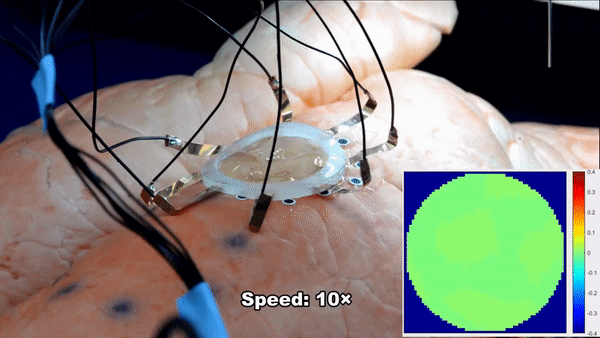
-
To demonstrate the capability to print multiple materials on a deformable target surface comprising a complicated geometry consisting of convex and concave features, colored silicone inks were printed on a deformable phantom face.
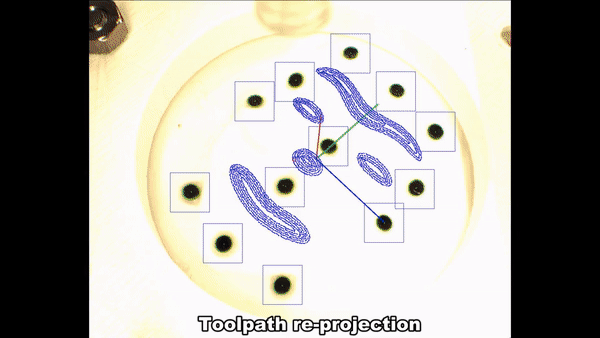